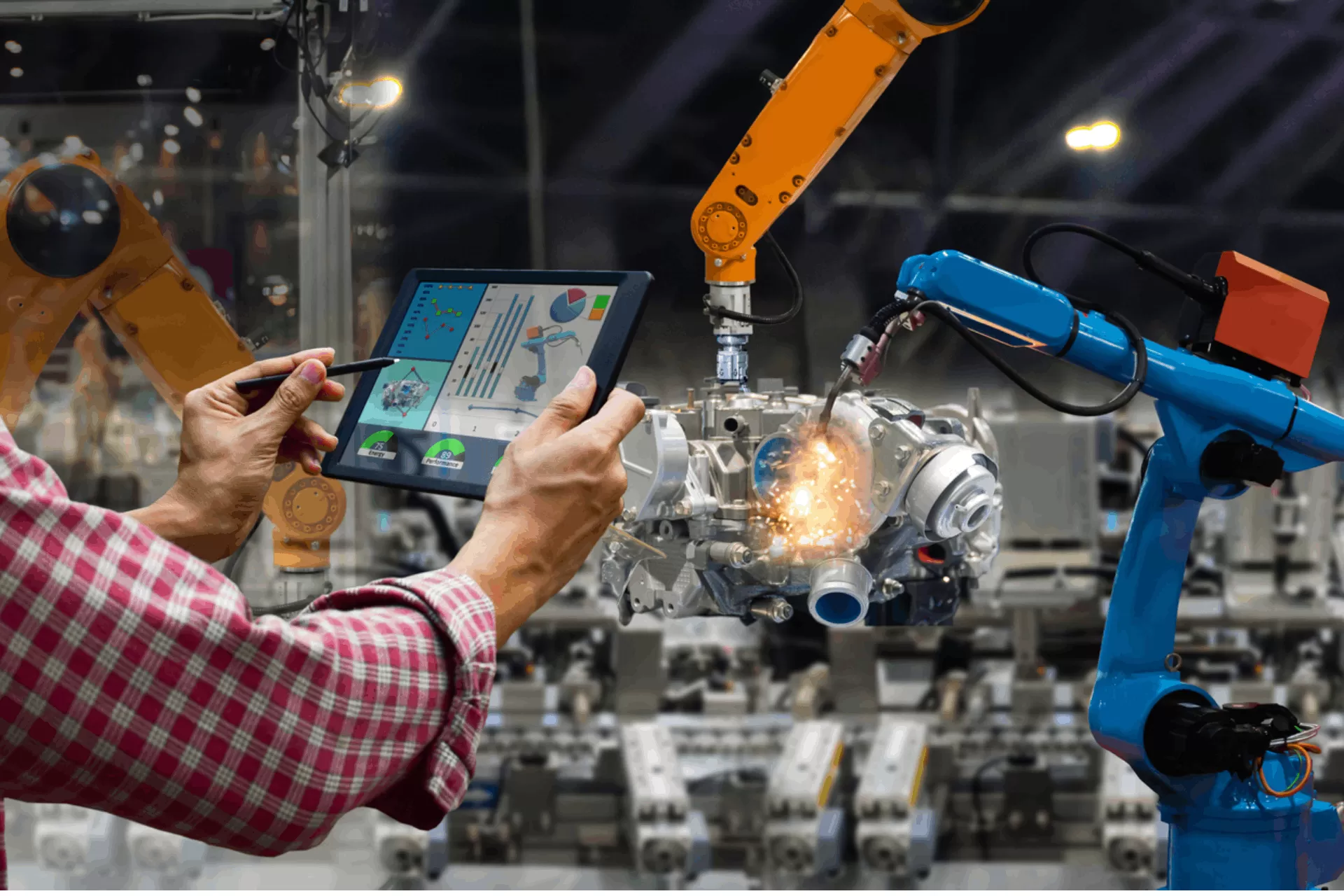
Are you making the most of Industry 4.0?
It is estimated that Industry 4.0 can create value of up to $3.7 trillion for manufacturers and suppliers by 2025. Yet, few organizations seem to have reaped the benefits of Industry 4.0 to its fullest. The disruptions and uncertainty brought in by COVID-19 have been a wake-up call for those companies that have not yet implemented the same while pushing those enterprises that have some -pilot use cases to think about deriving value from Industry 4.0 at scale.
According to a McKinsey report, post the pandemic, 26 percent of companies claimed to have fully scaled Industry 4.0 compared to 44 percent the previous year. This could be because of two reasons – one, the bar for fully scaled Industry 4.0 has risen to include the amount of business resiliency it can provide; and two, when organizations tested their Industry 4.0 platforms, it may have shown that they have further to go than they thought before their implementations are truly, fully scaled. Regardless of the reason, implementing and deriving value from at scale has become imperative. This is because 96 percent of organizations with fully scaled Industry 4.0 were able to respond to the pandemic in a timely and efficient manner as opposed to 19 percent of companies that had no implementation or 40 percent of enterprises that had implemented some use cases.
The imperative to adopt Industry 4.0 at scale is clear, yet there is a lack of clearly stated guidelines to make this possible. As a result, most organizations get stuck after implementing a few successful pilot projects and experience innovation fatigue. This article guides readers to lead their enterprises toward a successful, scaled Industry 4.0 implementation. Here are a few essential pointers to keep in mind:
-
Focus on key value drivers: Industry 4.0 has a wide range of applications, from shop-floor optimization to enhancing customer experience. This often leads to organizations launching a host of pilot projects without proper planning or business goals in mind. This machine-gun approach results in limited value being captured by Industry 4.0, innovation fatigue, and flagging employee interest. Organizations must therefore focus on what creates value instead of how the most cutting-edge technologies might be implemented. They must prioritize company-specific key value drivers that will allow them to demonstrate impact from Industry 4.0 within a short period.
-
Have a strategic roadmap: To implement Industry 4.0 at scale, one needs to identify its most pressing business problems, articulate its desired future, and develop a nuanced perspective on which technologies could address them. The company needs to comprehensively assess processes (including operations, supply chain, and product life cycle), technology (automation, connectivity, and intelligence), and organization (talent-readiness) to measure its Industry 4.0 readiness and maturity levels. Basis these parameters, the company can create a detailed plan to implement Industry 4.0 and leverage its implementation to achieve business goals.
-
Look for sustainable long-term wins: It is okay to focus on quick wins during the initial implementation and pilot phases. Quick wins usually come from improving operational effectiveness, but the benefits soon plateau. To enjoy sustained value from Industry 4.0, organizations must look at long-term wins by exploring new business models. Industry 4.0 has given rise to four major business models: as-a-service business model, platforms/ecosystems, IPR-based revenue models, and data-driven business models. Explore these models in the context of your organization and identify Industry 4.0 use cases that can enable the new business models.
-
Learn from other industries: When it comes to Industry 4.0 implementation, we observe a significant difference in maturity levels across various industries. For example, the automotive sector reports the most significant progress in the at-scale application, while energy and materials companies and consumer packaged goods (CPG) players report the least. Hence, do not be afraid to look outside your industry for digital best practices. Say, a CPG player looking to improve its manufacturing flexibility could look at the solutions developed by the automotive suppliers.
-
Pilot with scalability in mind: Quick fixes and temporary workarounds can accelerate the early implementation of digital solutions, but such projects often need time-consuming reengineering work to scale. This is particularly applicable to developing the right technology infrastructure for Industry 4.0 implementation. There is a limit to ignoring the weaknesses of a legacy IT/OT infrastructure. For scalable Industry 4.0 implementation, one needs a fully integrated industrial automation stack.
-
Engage the organization: Industry 4.0 is as much about people as technology. One can only scale Industry 4.0 by leveraging the organization’s domain and process expertise and sustainably building up new skillsets and capabilities. An organization-wide mandate coming from the leadership, investment in the right talent pool, regular communication of interim results, and executive sponsorship are fundamental to a successful transformation.
With the COVID-19 pandemic exerting significant cost pressure on businesses, it is tempting to pause or even stop the implementation of Industry 4.0 at scale. But this will do more harm than good, as seen over the last two years. For most organizations, doubling down on Industry 4.0 is the only way to remain relevant, sustainable, and profitable.